Maintenance of pneumatic systems
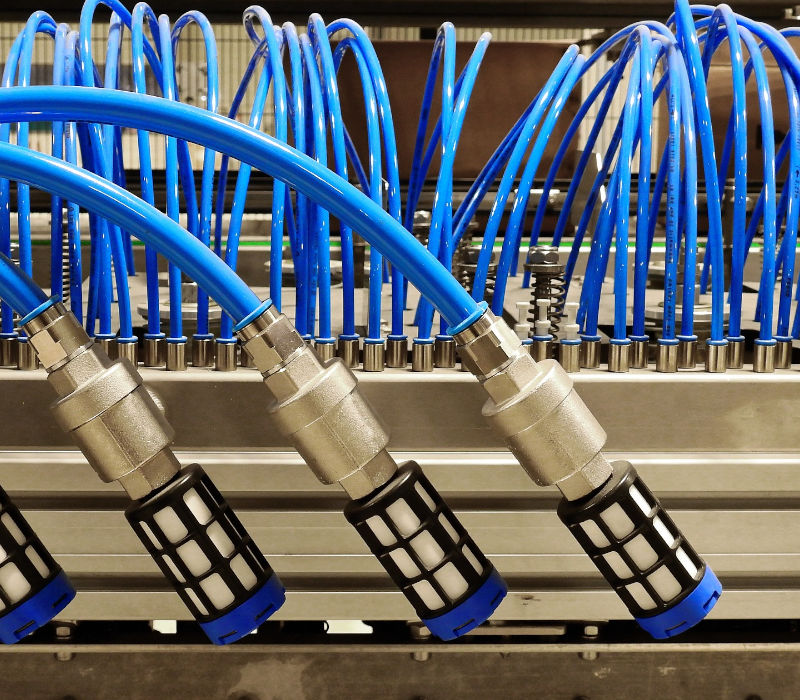
Maintenance and proper servicing of pneumatic systems, as with all systems, is essential to keep them working. In order to avoid unnecessary downtime, premature wear, accidents and unplanned replacement of system components; a few important steps need to be taken.
For a long-lasting system, it is essential to use an air preparation unit to ensure that the air entering the system is free of any harmful substances, such as moisture or dust, thus protecting the system parts from corrosion, clogging and loss of performance. Such devices are able to supply the air with useful substances that promote the long-term operation of pneumatic system components; working cylinders, grippers, fittings, throttle and check valves, connectors and other parts of the system. Such material may include oil specifically used for pneumatic systems, which can be injected continuously into the system. Lubrication is needed to ensure that most components, especially the sliding parts, are lubricated. The benefits of lubrication also include a potential descaling or rust-remodelling effect, which may be useful if the use of an air preparation unit has been neglected but a problem has been detected. The use of an air preparation unit can add many years to the life of certain elements of the system, but we must also ensure that this unit also requires regular attention, its components need to be checked and cleaned to perform its function. The air preparation unit includes filters, filter regulators, lubricators, dryers, pressure boosters, manometers, of which the filter requires the most attention and is the most visible indicator of air quality and system status. As part of ongoing maintenance, filters should be cleaned on a weekly basis, depending on the load on the machine. On a monthly basis, we need to make sure that moisture is being filtered out of the system, that there is enough oil in the preparation unit and that there are no air leaks in the system. It is most often at the connecting elements that air can escape involuntarily. At such points, a little soapy water is a simple way of checking for leaks.
Once the previous steps are in order, clean all parts and receivers, then lubricate the moving parts with a lubricant that facilitates movement. At average operation and load, a complete replacement of the air filters is also recommended every six months.
Once the air quality is OK and your pneumatic system is working with the right quality of air, it's worth taking a look at the pressure in the system. It is important to ensure that the system is only used within the pressure range that is appropriate for the parameters of all components. In most cases, the pressure of the pneumatic system is between 2 and 10 bar, but there are parts that can be damaged above 6 bar, but will work perfectly well at pressures as low as 0.5 bar. Before installation, it is important to check the operating and cracking pressure data and parameters of the system components, and if necessary, use a choke valve or pressure regulator in front of the device to reduce the pressure that can be applied to the device. In the long run, it is most economical to find the minimum pressure at which the system will work perfectly. This has a positive effect on both our energy consumption and the lifetime of the system components.
The maintenance and inspection of pneumatic work cylinders can also be a delicate and sometimes dangerous task. Here too, important steps should not be overlooked; turn off the power and then bleed off any remaining air pressure. Then we can carry out the maintenance process on the working cylinders. It is worth checking the condition of the seals and pistons in the tool, replacing them if necessary. One of the most common - but also one of the cheapest to repair - faults in pneumatic work cylinders is the wear of seals. Once everything is in order, lubricate the tool. After a comprehensive inspection, making the necessary replacements and assembling the tool properly, turn the power sources back on and test the sealing and operation of the part under low air pressure. Once you are sure that the air is not escaping anywhere and that the working cylinder is functioning properly, the last step is to carry out a test at working pressure. If no abnormalities are found here, it is very certain that the job has been done properly.
If we constantly monitor the condition of the system, and know the installation and commissioning dates of the system components, we can know which components are close to wear and tear, or to the end of their service life. This is important because the operating time and condition can be used to predict the approximate time of failure or inoperability of a given device. Of course, it's best to replace when the system is not in use, so it doesn't go out of service during use - no unexpected downtime and loss of production. Preliminary signs of impending failure may include slow operation, slow or choppy movement when the system requires more pressure to operate than before, unusual hissing noises or sluggish, intermittent starts.
It is important to ensure that workers are safe during both control shutdowns and maintenance, to prevent accidental machine start-ups and to exclude sudden energy release through the use of LOTO devices. If, during work, the system is pressurised without all the sub-assemblies being securely in place or the mechanical moving parts not being properly secured, it is easy to damage parts of the system or, in serious cases, cause an accident. The LOTO system devices ensure that the system cannot be accidentally started or pressurised without the consent of the maintenance staff. This is done by excluding all energy sources and possible start-ups during the repair process.
If all the necessary checks are carried out regularly and the above steps are taken at regular intervals, you can be sure that you have maximised the lifetime of your system and ensured its safe and long-term operation.