Advantages of shock absorbers, their selection
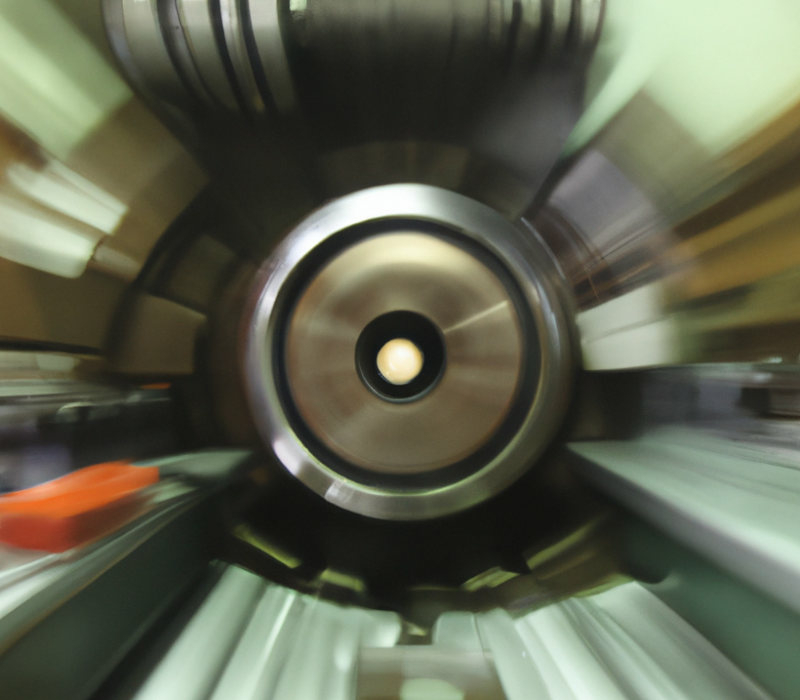
Shock absorbers play a vital role in maintaining the smooth, long-term, safe operation of industrial machinery. In this article, we will dive into the operation of shock absorbers and the benefits of their use in industrial machinery, and try to help you consider the parameters you need to take into account.
Why do you need a shock absorber?
During the operation of the machines, the energy from the working surface affects the frame and other parts of the machine. As the machine does the work we want it to do, it is subject to an opposing force that causes the machine to vibrate. Machines used in industrial machinery, but especially in construction, manufacturing and mining, can be subjected to a variety of harsh operating conditions, such as rough terrain, heavy loads and extreme temperatures. Without proper shock absorption, these machines can experience excessive vibration, which can lead to structural damage, component failure and reduced efficiency. These devices help us to dampen these vibrations and shocks in order to ensure the longest possible service life for our machines.
What are the benefits of using shock absorbers?
Shock absorbers help control vibrations and provide greater stability, improving the overall performance and efficiency of the machine. In addition, by reducing the amount of vibration transmitted to the operator, they improve operator comfort and reduce the risk of operator fatigue. Shock absorbers help protect the machine and its components from excessive wear, which can extend the life of the machine and reduce maintenance costs. By reducing wear and tear on the machine and its parts, shock absorbers can help reduce maintenance costs and increase the overall reliability of the machine.
The pneumatic shock absorber
Pneumatic shock absorbers work on the principle of compressed air. They consist of a piston and a cylinder filled with compressed air, which work together to absorb and dampen shocks and vibrations. The piston is connected to the machine, which moves in response to the shock/vibration. This movement compresses the air in the cylinder, which acts as a spring, absorbing the energy of the shock and reducing its transmission to the rest of the machine. When the shock or vibration subsides, the compressed air in the cylinder expands and pushes the piston back to its original position. This compression and expansion cycle takes place rapidly and continuously, ensuring that shocks and vibrations are effectively damped. The speed of the shock absorber reaction can be adjusted by varying the pressure of the compressed air in the cylinder.
One of the advantages of pneumatic shock absorbers is that they provide reliable and consistent performance in a wide range of conditions. They can cope with a variety of loads and are unaffected by temperature changes or moisture, making them a popular choice for use in extreme industrial environments.
How to choose the right shock absorber for the application?
When choosing a shock absorber for industrial applications, there are a number of factors to consider:
- Load capacity: shock absorber load capacity: determine the weight of the moving object and choose a shock absorber with a load capacity greater than the weight of the object.
- Stroke length: take into account the maximum movement or distance that the shock absorber can handle. Stroke length should be selected based on the maximum distance that can be absorbed by the shock absorber.
- Number of cycles: take into account the frequency of shock absorber use. Frequently used shock absorbers should be more durable than less frequently used shock absorbers.
- Environment: monitor the operating environment; for example, temperature and humidity. Choose a shock absorber that is designed for the conditions.
- Mounting method: select the appropriate mounting method for your application. Several mounting options are available; threaded mounting is most often preferred.
To summarise, shock absorbers are a critical component of industrial machinery and their use can bring many benefits; improved stability, greater operator comfort and safety, increased machine life and reduced maintenance costs.