The main causes of pneumatic cylinders failures
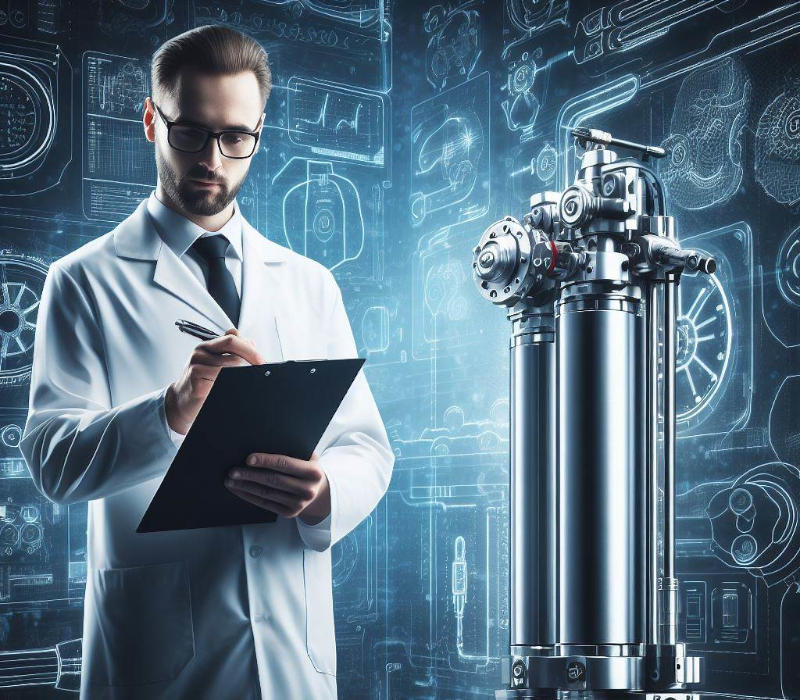
Depending on the complexity of a pneumatic system, it can be made up of many components, so it is important to know your system, to be aware of its weaknesses and to know which ones need special attention and improvement. But what are the basic weaknesses of a pneumatic system?
Pneumatic systems use compressed air to create mechanical movement, thus doing useful work. It is the power cylinders that perform the energy conversion process, they do the work, and it is these devices that are subjected to the greatest stress. If these tools fail, it will cause production stoppage and loss of revenue. To avoid this, we have collected the most important causes that lead to the failure of working cylinders.
The first cause is the clogging of the actuators by contaminants from the system that are deposited in the actuator cylinders. These impurities slow down the flow and can even cause the machine to stop completely. A similar problem, which can lead to a stoppage of the cylinder, can be caused by excessive moisture in the system, which can lead to corrosion. Moreover, if moisture and dirt are present at the same time, the moisture mixed with the accumulated dirt will result in a larger volume of undesirable material, which will lead to clogging even more quickly.
The second main source of problems is related to tightness. It is important to check the seals in your machines regularly, as they wear out over time and if the seals are not doing their job properly, your cylinder can easily fail.
The above two causes: leakage and clogging are signs that the device requires more energy to do its job than before. These problems need immediate remedial action, because if they continue to malfunction or even become stuck, they may suffer fatal damage that can no longer be repaired by installation or repair, and may even require complete replacement of the device, which can be costly and, in the worst case, costly in terms of lost purchasing time.
The third reason is an inappropriate choice of load. When choosing cylinders, it is important to know how much load they will be subjected to. If we know this with absolute certainty, we should choose a cylinder that can carry up to twice the assumed load. This means that you don't have to use the tool to its maximum capacity and push it to its limits, so that you can operate your tool more efficiently and for longer periods of time, not to mention that it can still perform its job without any problems in the event of an increase in production.
The most common sign of improper load selection is damage to the working cylinder during operation that is not caused by an external factor. A common consequence is that a part of the cylinder is displaced and the displaced part causes damage to the cylinder. Other signs of displacement of the internal parts of the cylinder are inadequate, inaccurate, possibly lateral movement of the rod or jamming of the rod. Internal misalignment may also be the cause of the problem if the device makes an unprecedented rattling, loud noise when operating.
When operating pneumatic systems, it is important to detect and correct problems as soon as possible. This will help to prevent breakdowns, earlier than planned shutdowns and unplanned downtime during operation.